In this blog post we will cover Order-Related Replenishment at Storage Type level with Rough Bin Determination.
Rough bin determination means the storage type must be written to the delivery item even if no stock exists. You specify that the storage type (without storage bin) is written to the source data of a delivery item, even if there is no stock for the product in the storage type. This enables you to use the order-related replenishment to perform replenishment for the pick storage type, since a requirement for picking occurs in this storage type as a result of this. If rough bin is not enabled, the storage type is generally not used if there is no stock for the product in that storage type.
Characteristics of Order-Related Replenishment:
◉ Like planned replenishment, it can be triggered either interactively or in the background
◉ It calculates replenishment quantities according to open warehouse request quantity
◉ It is started when stock figure is lower than the required quantity
◉ It rounds up to multiples of minimum replenishment quantity
◉ Exceeding maximum quantity is possible
◉ The goal in order-related replenishment is to ensure that open outbound deliveries can be fulfilled. This is the only strategy in which the maximum quantity can be exceeded with replenishment.
Fig 1. Order-Related Replenishment
In our scenario, our picking Storage Type will be ZLW1 and we will replenish this storage type from Storage Types S970, SF01 and Z001.
Master Data Setup:
1. Define Rough Bin Determination for Storage Type ZLW1 and Replenishment Level as Storage Type Level: Supply Chain > Warehouse Management > Master Data > Maintain Storage Types:
Fig 2. Maintain Storage Types
2. Define Rough Bin determination for the picking Warehouse Process Type: Supply Chain > Warehouse Management > Cross-Process Settings > Define Warehouse Process Type:
Fig 3. Define Warehouse Process Types
3. Activate Order-Related Replenishment Strategy for Storage Type ZLW1 and assign the replenishment WPT: Supply Chain > Warehouse Management > Internal Warehouse Processes > Activate Replenishment Strategies in Storage Types:
Fig 4. Activate Replenishment Strategies in Storage Types
4. Define replenishment quantity in the product master: this setting defines what is the minimum quantity for the replenishment WT, and the min. and max. replenishment quantity in the storage type. For example, if the minimum replenishment quantity is 5 PC the system will not create any task for less than 5 PC and only for multiples of 5 (5, 10, 15, and so on).
Since we’re not using fixed bins, we need to enter the replenishment quantity here in the product master at storage type level.
“Maximum Quantity” is a mandatory field to make the scenario works, note that maximum quantity can be exceeded.
“Minimum Quantity” is recommended if you always want to leave some products in the picking storage type.
“Minimum Replenishment Quantity” is recommended if you want to have a minimum quantity in the WT, if left empty system will use the smallest unit of measure as minimum quantity.
You define it in Manage Product Master Data app > Warehouse Management > Warehouse > Storage Type > Replenishment
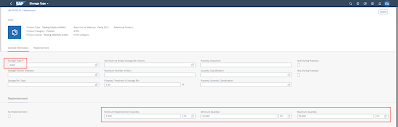
Fig 5. Replenishment at Storage Type level in Product Master Data
Additional customizing:
To assign our custom picking WPT to the delivery item, we need to create a Control Indicator for WPT determination, assign it to the Warehouse Process type and assign it to the product in the product master.
1. Supply Chain > Warehouse Management > Cross-Process Settings > Define Control Indicators for Determining Warehouse Process Types: Allows you to define control indicators for products, which you can then use to group products for warehouse process type determination.
2. Supply Chain > Warehouse Management > Cross-Process Settings > Determine Warehouse Process Type: Allows you to define settings for the system to automatically determine the warehouse process type for a warehouse request.
Fig 6. Determine Warehouse Process Type
Here it means Document Type LO + Control Indicator Z1 will assign WPT LWPK to the delivery item.
3. Manage Product Master Data app > Warehouse Management > Warehouse
Fig 7. Process Type Determination Indicator in Product Master Data
Scenario overview:
Physical Stock: We only have stock available in Storage Type S970
Fig 8. Warehouse Monitor app
Outbound Delivery Overview: Outbound Delivery Order created for 40 PC, WPT LWPK was assigned
Fig 9. Warehouse Monitor app
Replenishment Procedure:
Call Replenish Stock app, fill in the necessary entries and Execute. Here, I’m planning replenishment for the entire ZLW1 storage type.
Fig 10. Replenish Stock app
On the next screen, check the proposed quantity to be replenished, select the line item and choose Perform Replenishment
Fig 11. Replenishment Proposal
The WT for replenishment is then created.
Fig 12. Warehouse Task creation log
No comments:
Post a Comment