We are “Bandleaders for the Process.” Our mission is to orchestrate plant operation, with leadership across the manufacturing value chain. This reminds me of my job in the plant 20 years ago.
One important mission was to manage engineering change; it required a lot of time and attention to plan, direct, control and track all the activities across the team with multiple files and paper documents:
◉ What is the impact of change?
◉ When will the new parts come from the suppliers? How many old parts do we have in stock?
◉ Which production order should be changed? What is the status of production orders?
◉ Are new tools ready? Have all of build package documents been revised?
◉ Who is working on MBOM? When will it be released?
◉ Do we have to disassemble parts?
◉ Have we properly recorded the new serial number during the re-assembly process?
The bandleader is vital to the success of implementing changes.
The factory of today looks very different from the one 20 years ago – more technologically advanced than ever. Machines interact with humans, advance production methods are implemented with autonomous machines, real time data from machines, sensors and devices is available, and AI is leveraged to create meaningful information and improve decisions.
However, many manufacturing companies still struggle to manage engineering change.
Data is managed in silos, handled in PLM, ERP, MES and more. Data entries get complicated. An extensive manual intervention is needed for continuous data transfers and sharing. Such manual processes are challenging and prone to errors. They can lead to significant operational inefficiencies and data inconsistency.
If your bandleaders don’t get a holistic view of the change process, they are trying to conduct without any sheet music. The answer is not to turn the process over to machines, human interaction is very important in orchestrating the whole production engineering change process. But by giving bandleaders access to more effective mechanisms, they can shine in our digital society, spend less time on manual activities and more time driving true value, and derive greater satisfaction from their work.
Data driven engineering change processes within SAP S/4 HANA Manufacturing
See how SAP S/4HANA Manufacturing for production engineering and operations (aka PEO) orchestrates the whole production engineering change process and scales up your Industry 4.0 by realizing a true digital continuity that connects critical data points across the enterprise.
The digital thread starts from PLM and all the product data, and updates are integrated into one single platform(PEO), encompassing all downstream processes, as seen in the following steps, from 1 to 8.
Step 1
Engineering snapshot is a change coordination package containing new updates of EBOMs plus corresponding 3D visuals and product manufacturing information(PMI) and triggers the production engineering process by creating a change record(CR).
Step 2
Change Record is a single entry point used to orchestrate the whole production engineering process required in a change cycle and keeps track of all changes. Manufacturing engineers can analyze, plan, and execute the changes to manufacturing BOMs, shop floor routings, production orders. And by leveraging workflows, get approvals from appropriate people.
Step 3
Change impact analysis identifies all manufacturing objects impacted by a change. Objects impacted by a change are viewed in a list or in a network view mode. The network provides insights on the relationships between the objects and enables a further drill down to see additional information. Impacted items, operations, and operation activities are highlighted to visualize. All necessary information has been collected and added to the change record. Production holds can be initiated to prevent operation activities from being started in case they are subject to change.

Step 4
Visual Enterprise Manufacturing Planner(VEMP) enables handover of engineering structure to the manufacturing structure. New versions of multi-level EBOM are viewed in sources panel and show the new components that are not assigned in current version of MBOM. Comparison highlights the difference and provides guidance to edit (add or delete) components in new version of MBOM with an interactive 3D visual. By reconciling the EBOM with the MBOM, it checks whether any component is over- or under-assigned.

Step 5
Production process planning is used to create shop floor routings that include all information needed for production planning, production costing, and shop floor execution. Operations are used for planning and costing purposes. Operation activities are used for shop floor execution and describe in detail how an operation must be performed: work instructions, data collection requirements, qualifications needed, PRTs, buyoff procedures.
In the change process, a new shop floor routing version is created and assigns a new MBOM version with corresponding 3D file. PMI data automatically then navigates to update objects required to change.
◉ New components are allocated to operation activities from the new MBOM component list referring to the 3D visual.
◉ Check PMI changes in auxiliary data workspace and can create and change inspection characteristics.
◉ Change tools for new components, new inspection procedures, PMI changes.
◉ Update interactive work instructions by replacing links to components, inspection characteristics, tools.
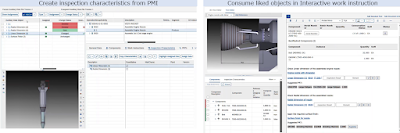
Step 6
Order change management is the ability to incorporate changes into an order that is currently in process. The built-in comparison capability allows the production engineer to identify all changes between the specified routing versions. This can be used to evaluate how further engineering changes can be applied to in-process production orders such as:
◉ Adding a new component
◉ Deleting an existing component
◉ Increasing or decreasing a component quantity
◉ Adding operation activities to instruct additional work
◉ Temporarily or permanently disassembling a component that has been fully or partially consumed

Step 7
Production Orders are executed with a comprehensive working environment for shop floor operators.
All changes are updated in real time so that shop floor operators can validate proper execution with latest work instructions and inductive 3D model.
In the disassembly process, the shop floor operator launches an operation activity and gets a view of “Components to be removed” and “Components to be re-assembled” as defined during the order change management.
Step 8
All information gathered during production is documented in the genealogy and production action log for each individual product. This provides a complete and detailed history of how a product has been produced and how an order has been executed. The multi-level As-Built Report provides a top-to-bottom view of all components used in production.
No comments:
Post a Comment